Why Routine Tank Welding Inspection is Crucial for Architectural Integrity
Why Routine Tank Welding Inspection is Crucial for Architectural Integrity
Blog Article
The Necessary Duty of Tank Welding Assessment in Ensuring Structural Integrity and Safety And Security Compliance in Industrial Applications
In the world of commercial applications, container welding examination emerges as a crucial component in safeguarding architectural stability and guaranteeing compliance with safety and security guidelines. Making use of a mix of methods such as aesthetic analyses and progressed screening methods, these examinations offer to identify and alleviate potential flaws before they intensify right into substantial threats.
Importance of Tank Welding Inspection
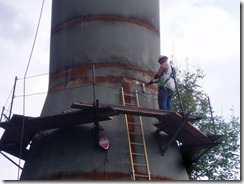
Ensuring compliance with industry criteria and policies is one more substantial element of storage tank welding inspection. Regulatory bodies mandate rigorous guidelines for the construction and maintenance of tank, and detailed examinations assist companies stick to these needs. Non-compliance can cause severe penalties, consisting of penalties and closures, even more highlighting the need for extensive inspection procedures.
In addition, tank welding inspection plays a crucial function in keeping functional effectiveness. In summary, the value of container welding evaluation exists in its capability to guard public health and wellness, shield the environment, and make certain compliance with regulative structures.
Key Evaluation Methods
Reliable tank welding evaluation depends on a variety of vital techniques that ensure detailed analysis of weld quality and structural stability. Amongst one of the most common techniques are aesthetic evaluation, ultrasonic testing, radiographic screening, and magnetic fragment testing - Tank Welding Inspection. Each method uses one-of-a-kind advantages in evaluating different elements of the weld
Aesthetic assessment functions as the very first line of defense, enabling assessors to determine surface flaws, irregularities, or inconsistencies in the weld bead. Ultrasonic screening utilizes high-frequency acoustic waves to spot internal imperfections, such as splits or spaces, giving an extensive analysis of weld stability. This method is particularly efficient in spotting issues that may not show up externally.
Radiographic screening makes use of X-rays or gamma rays to create photos of the welds, revealing interior gaps and providing a permanent record for future reference. This method is very reliable for important applications where the danger of failing should be minimized.
Finally, magnetic particle testing is used to determine surface area and near-surface problems in ferromagnetic products. By applying magnetic areas and great iron bits, examiners can determine interruptions that may endanger the structural stability of the tank. Together, these strategies form a durable framework for ensuring top quality welds in industrial applications.
Compliance With Safety And Security Standards
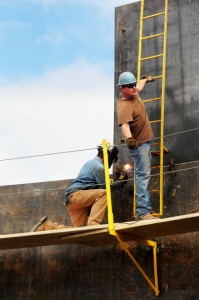
Routine examinations play a crucial function in guaranteeing compliance by identifying potential failings or deviations from recommended criteria. Examiners are educated to assess weld high quality, validate product requirements, and assess the total architectural honesty of storage tanks. Their competence is crucial in making sure that welding procedures satisfy the called for safety and security criteria.
Moreover, compliance with security standards not only shields workers yet additionally safeguards the setting from possible threats such as leaks or disastrous failings. Organizations that focus on safety and security compliance are much better positioned to minimize dangers, boost operational effectiveness, and foster a society of safety and security within their workforce. In recap, maintaining extensive compliance with security requirements is important for the effective procedure of tank welding activities in commercial setups.
Advantages of Routine Inspections
Regular examinations are indispensable to keeping look at this web-site the architectural honesty and safety and security of bonded containers. These examinations supply a methodical approach to recognizing possible problems or weaknesses in the welds, guaranteeing that any kind of issues are addressed before they rise right into significant failings. By performing regular evaluations, organizations can identify deterioration, exhaustion, and various other forms of deterioration that might endanger container efficiency.
Moreover, constant assessments contribute to conformity with market guidelines and standards. Sticking to these standards not just mitigates lawful dangers however additionally boosts the organization's reputation for safety and security and reliability. Normal inspections cultivate an aggressive security culture, urging workers to additional reading identify and prioritize the value of equipment honesty.
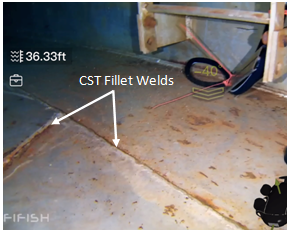
Situation Research Studies and Real-World Applications
Study and real-world applications highlight the concrete effect of efficient tank welding evaluation techniques. One significant instance is a large petrochemical center that faced significant functional disturbances as a result of leakages in tank. Complying with the implementation of rigorous welding inspection protocols, including aesthetic and ultrasonic testing, the center determined crucial problems in weld joints that could have resulted in catastrophic failures. This aggressive technique not only stopped ecological dangers but also conserved the company millions in potential cleaning prices and regulatory fines.
In a similar way, a water therapy plant executed a comprehensive assessment program for its storage tank welding procedures - Tank Welding Inspection. By including non-destructive screening techniques, the plant had the ability to detect early indicators of deterioration and fatigue in weld joints. This prompt treatment extended the life-span of the storage tanks and guaranteed conformity with safety and security policies, thus protecting public health
These instance researches underscore the relevance of normal and systematic container welding inspections. By focusing on these methods, sectors can mitigate threats, enhance structural integrity, and ensure compliance with safety and security standards, inevitably causing boosted functional effectiveness and decreased responsibilities.

Final Thought
In final thought, container welding inspection is an essential component of maintaining structural honesty and security in industrial applications. Utilizing various evaluation methods ensures early discovery of potential flaws, thus protecting against tragic failures.
Report this page